Last updated on May 5th, 2025 at 06:45 pm
In an increasingly globalized economy, procurement risk management is more critical than ever for facilities management. Facilities rely on interconnected supply chains and third-party vendors to source essential services, equipment, and materials needed for operations. Without a robust procurement risk management strategy, facilities are vulnerable to various threats—from supply chain disruptions to compliance failures, safety issues, and financial instability.
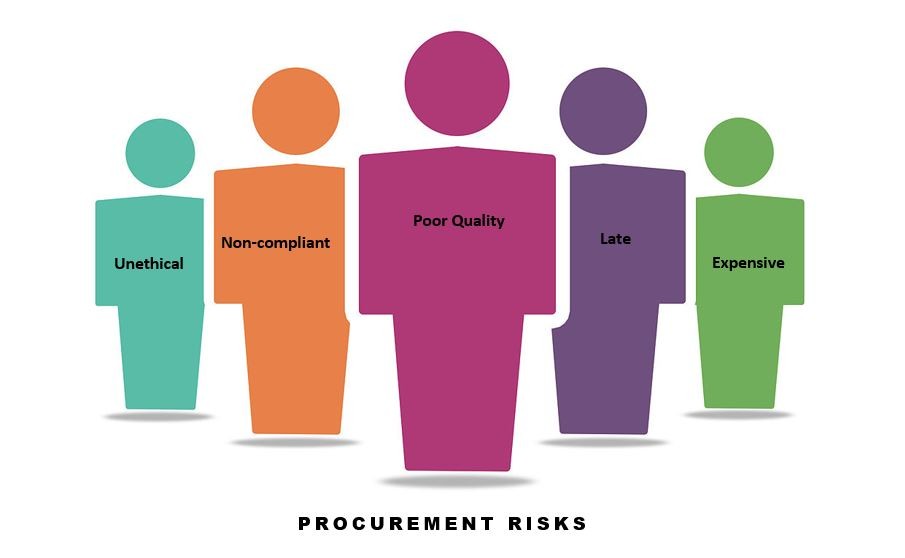
This guide explores what procurement risks mean for facilities management, why procurement risk management is vital for facilities teams, the top procurement risks faced by facilities, and actionable strategies to minimize these risks. Whether you’re a facilities manager or business leader, understanding and addressing procurement risk is key to ensuring smooth operations, cost-efficiency, and long-term success.
What Is Procurement Risk Management?
Procurement risk management involves identifying, assessing, and mitigating risks that could negatively impact a company’s ability to acquire essential products, resources, or services. These risks range from supplier failures and price volatility to compliance breaches and inaccurate demand forecasting.
According to McKinsey, procurement risks can be broadly categorized into:
- Product shortage risk: Failing to procure required products in the necessary quantity.
- Supplier risk: Working with unreliable or unethical vendors who affect performance.
- Inflation risk: Facing unexpected spikes in product pricing.
Procurement risk management aims to proactively address these vulnerabilities to ensure smooth business operations and cost efficiency.
Why Is Procurement Risk Management Important?
Effective procurement risk management is not a luxury—it’s a necessity. Here are several reasons why it plays a pivotal role in business continuity:
- Cost Control: Businesses can save 11–20% through increased transparency and smarter sourcing.
- Improved Vendor Relationships: Strong risk management enhances communication and trust with suppliers.
- Operational Continuity: Reduces the chance of supply chain disruptions.
- Regulatory Compliance: Ensures that vendors meet legal and ethical standards.
- Customer Satisfaction: Reliable procurement ensures timely product delivery and service excellence.
13 Common Procurement Risks to Watch
To build an effective procurement risk strategy, it’s crucial to understand the key threats organizations face:
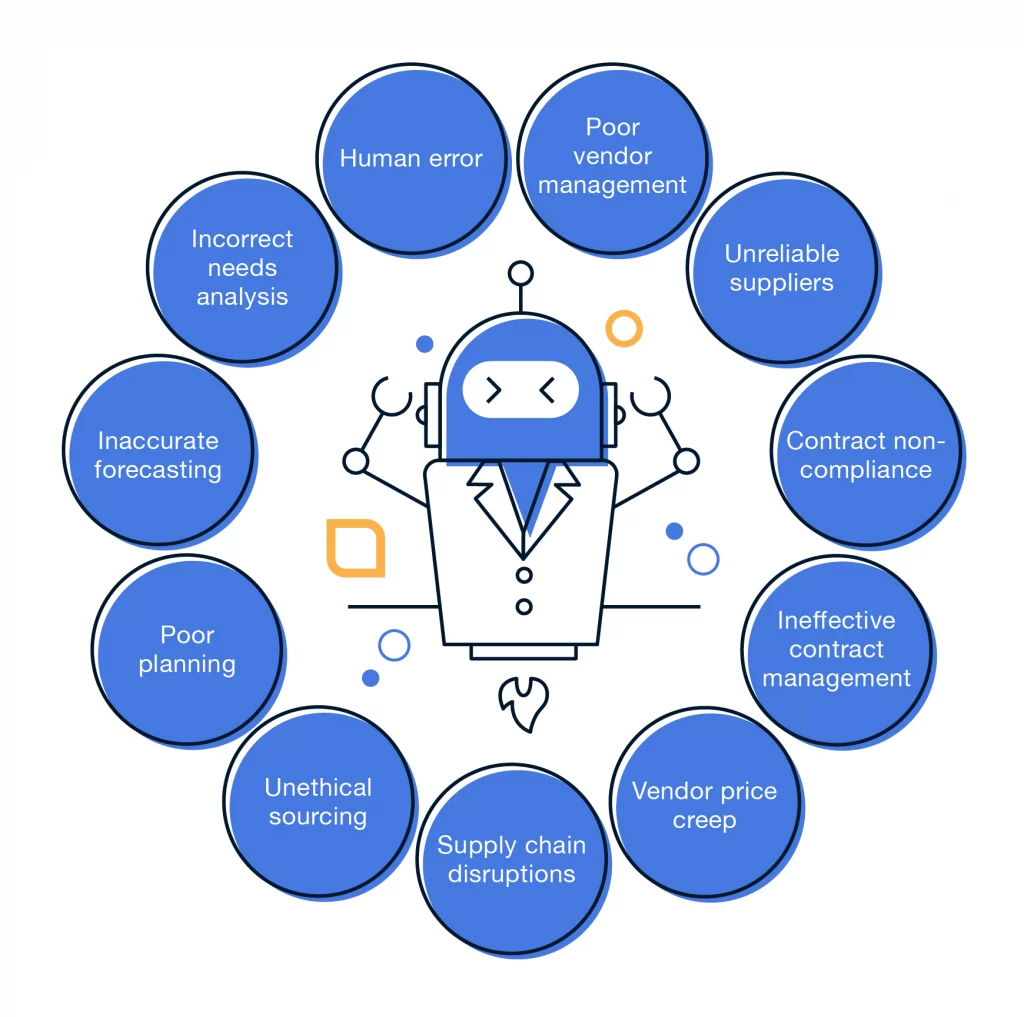
- Inaccurate Internal Needs Analysis: Poor analysis leads to over- or under-ordering and wasted resources.
- Poor Vendor Sourcing: Working with vendors lacking transparency, stability, or compliance poses serious risks.
- Ineffective Vendor Onboarding: Missing documentation or expectations causes delays and confusion.
- Inadequate Vendor Management: Without proper oversight, it’s difficult to measure vendor performance.
- Price Instability: Fluctuations in pricing due to market or geopolitical factors strain budgets.
- Resistance to Digitalization: Hinders e-procurement adoption, reducing efficiency and increasing manual errors.
- Supply Chain Disruptions: Natural disasters, political unrest, or pandemics can halt operations.
- Manual Procurement Processes: Reliance on spreadsheets leads to data errors and inefficiencies.
- Inaccurate Forecasting: Leads to inventory shortages, higher costs, and operational delays.
- Compliance Management Failures: Results in legal issues and damaged reputations.
- Budget Overspend: Poor planning and lack of oversight can cause financial strain.
- Talent Shortages: Lack of skilled procurement professionals reduces process effectiveness.
- Inefficient Contract Management: Unmonitored contracts result in missed deadlines, non-compliance, or legal issues.
How to Manage Risks in Procurement Management
Managing risk in procurement can be challenging due to uncertainty around which risks may occur and their potential impact. A simple yet effective risk management process involves five key steps:
1. Risk Identification
Begin by identifying potential procurement risks. This includes internal (micro) factors such as changes in company strategy or structure, and external (macro) factors like environmental, economic, technological, political, legal, and ethical risks. Involving cross-functional teams helps provide a broader perspective.
2. Risk Analysis
Analyze each identified risk using qualitative, semi-quantitative, or quantitative methods. Choose the approach based on the complexity, cost, and availability of data. The goal is to understand the nature and potential consequences of each risk.
3. Risk Assessment
Evaluate the likelihood and impact of each risk. Categorize them (e.g., high, medium, low) and determine what is currently being done to manage them. Ask critical questions such as:
- What are the most concerning risks?
- What mitigation measures are in place?
- How effective are current controls?
4. Action Plan
Develop actionable steps to address the prioritized risks. This may include:
- Risk avoidance
- Risk transfer (e.g., through insurance)
- Risk sharing with suppliers
- Risk reduction by improving controls
Clearly define roles and responsibilities and ensure stakeholder alignment during implementation.
5. Monitoring
Continuously monitor risks, as they evolve over time. Establish procedures for reporting and managing emerging risks. Regular reviews help maintain an up-to-date risk profile and keep the mitigation strategy relevant.
7 Effective Strategies to Minimize Procurement Risks
Minimizing procurement risks starts with proactive planning and investment in digital tools. Here are seven actionable tips:
1. Standardize Procurement Processes
Standardization eliminates ambiguity and improves efficiency. Establish company-wide policies on vendor assessments, budget reviews, internal needs analysis, and contract approvals to ensure consistency.
2. Automate Manual Tasks
Automate vendor management, contract tracking, invoicing, and purchase orders to reduce errors, save time, and ensure compliance.
3. Strengthen Vendor Relationships
Transparent, ongoing communication with suppliers builds trust and ensures performance alignment. Create mutual KPIs and performance metrics to measure outcomes.
4. Embrace E-Procurement Solutions
Digital procurement tools help manage spend analytics, automate workflows, and improve decision-making. These tools streamline processes and increase supply chain visibility.
5. Invest in Digital Adoption Platforms
Training your team and partners to use procurement technology effectively is crucial. Digital adoption platforms like Whatfix offer in-app guidance and tutorials, ensuring proper tool usage and higher ROI on software investments.
6. Prioritize Communication
Poor communication is a root cause of many procurement issues. A centralized system for data and messages ensures everyone is on the same page.
7. Track and Monitor Supplier Performance
Use KPIs like lead time, compliance rates, defect rates, and on-time delivery to continuously assess and improve vendor reliability.
The Role of Technology in Procurement Risk Management
The future of procurement lies in digitization. Manual processes no longer suffice in today’s dynamic business environment. E-procurement and source-to-pay (S2P) platforms improve efficiency, reduce errors, and provide real-time visibility into procurement activities.
Whatfix, for instance, supports procurement teams by integrating with tools like SAP Ariba and Coupa to provide real-time help and process analytics. By enabling end-users with guided workflows, companies can:
- Improve system adoption
- Enhance compliance
- Reduce procurement cycle times
- Eliminate guesswork
Procurement Risk Management & Facility Management: A Smart Integration
Procurement risk management doesn’t exist in a vacuum—it intersects with other critical business areas, especially facility and asset management. Integrating procurement with facility management software enhances visibility into asset life cycles, ensures timely maintenance, and reduces operational risks.
This is where Facility Bot, the best facility management software in Singapore, plays a key role. By linking fault reporting and asset tracking to procurement workflows, Facility Bot enables companies to:
- Automatically generate procurement requests from fault reports
- Ensure spare parts and services are available when needed
- Track supplier performance in the context of facility needs
- Centralize vendor data, contracts, and maintenance schedules
Facility Bot’s automation and integration capabilities provide a seamless experience that strengthens procurement risk management and ensures business continuity.
Final Thoughts
Procurement risk management is essential for every organization looking to thrive in today’s unpredictable global market. From supplier vetting and onboarding to performance tracking and contract automation, businesses must be equipped with the right tools and strategies to mitigate risk.
With digital solutions, standardized workflows, and integrated facility management tools like Facility Bot, your organization can stay ahead of procurement risks and operate with confidence.
Looking to elevate your procurement and facility processes? Discover why Facility Bot is considered the best facility management software in Singapore.